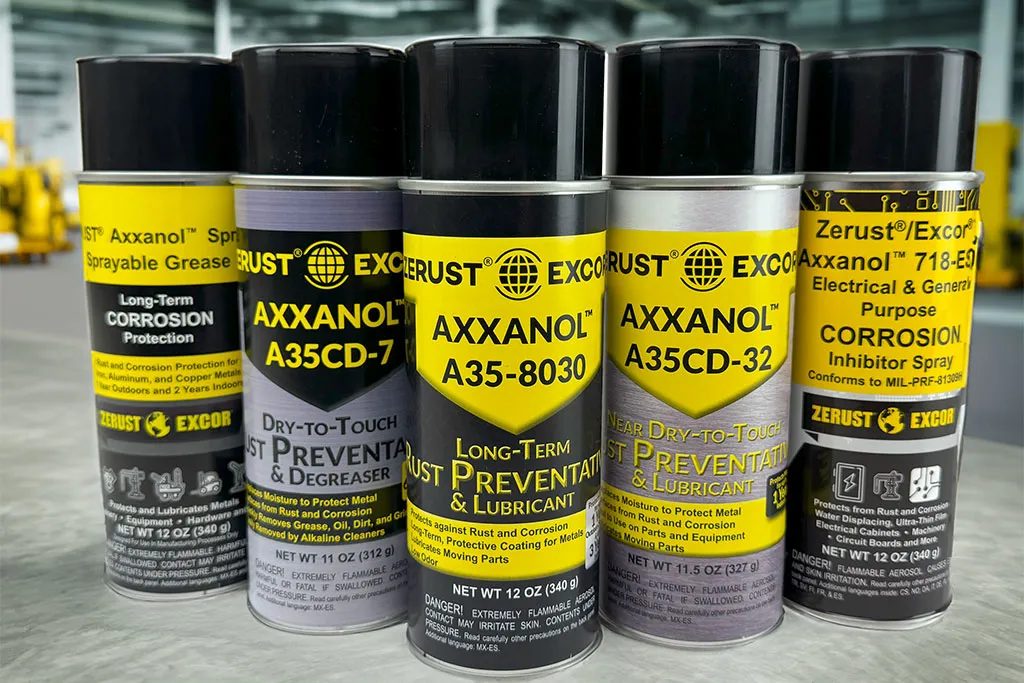
Protect Metal Assets with Confidence Using ZERUST® Aerosol Rust Preventatives
When your metal parts, assemblies, or equipment are at risk of rust, fast and reliable protection is essential. ZERUST® aerosol rust preventative products offer a clean and convenient way to protect your valuable assets from corrosion during shipment, storage, or operation. ZERUST® offers a complete line of aerosol rust preventatives designed to meet the needs
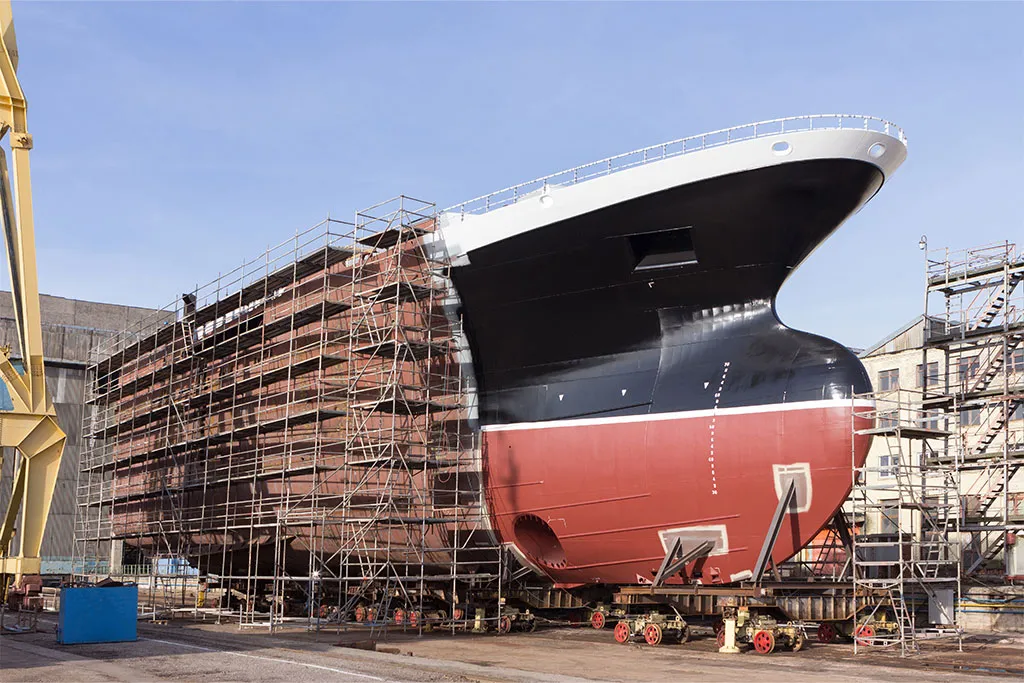
Corrosion Protection in Shipbuilding: Integrated Strategies for Long-Term Performance
Corrosion protection in shipbuilding is a critical part of ensuring vessel integrity, safety, and operational efficiency. From steel hulls to electrical enclosures, components are constantly exposed to harsh conditions, including salt-laden air, humidity, and temperature fluctuations. Consequently, these parts face a high risk of corrosion. To meet these challenges, modern shipbuilders rely on a combination
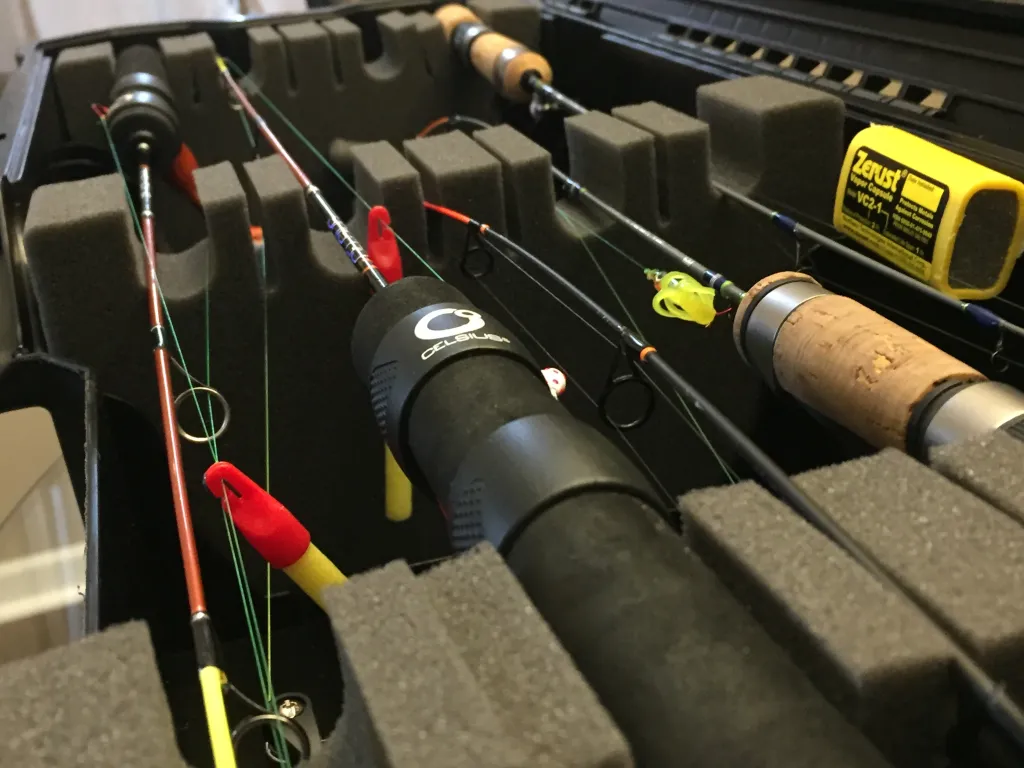
How ZERUST® Products Prevent Rust in Everyday Life
Typically, when most people think of ZERUST® products, they picture them in use on factory floors, in shipping crates, or in industrial applications. And while ZERUST® has certainly made its mark protecting large-scale metal assets around the globe, its products are equally at home in everyday life. From your garage to your gun safe, your
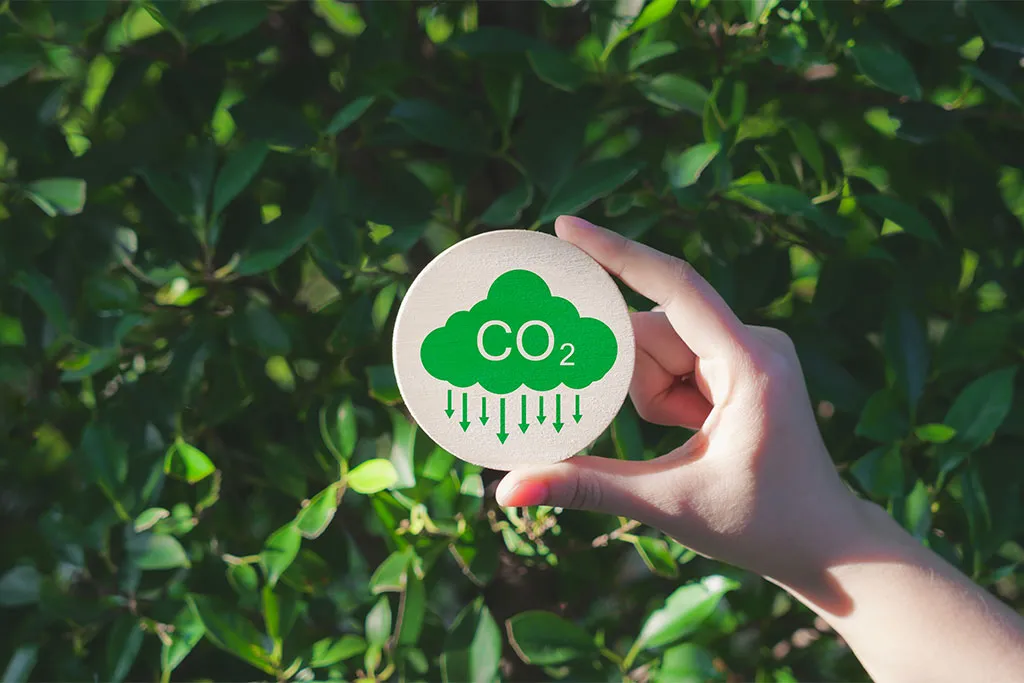
How ZERUST® Helps in Reducing Carbon Emissions
Sustainable VCI Solutions: A Step Toward Reducing Carbon Emissions Reducing carbon emissions is a global priority. Businesses are seeking innovative solutions to minimize their environmental impact. ZERUST®, a division of Northern Technologies International Corporation (NTIC), is leading the way with sustainable Vapor Corrosion Inhibitor (VCI) technologies. These solutions extend the life of metal components, reduce
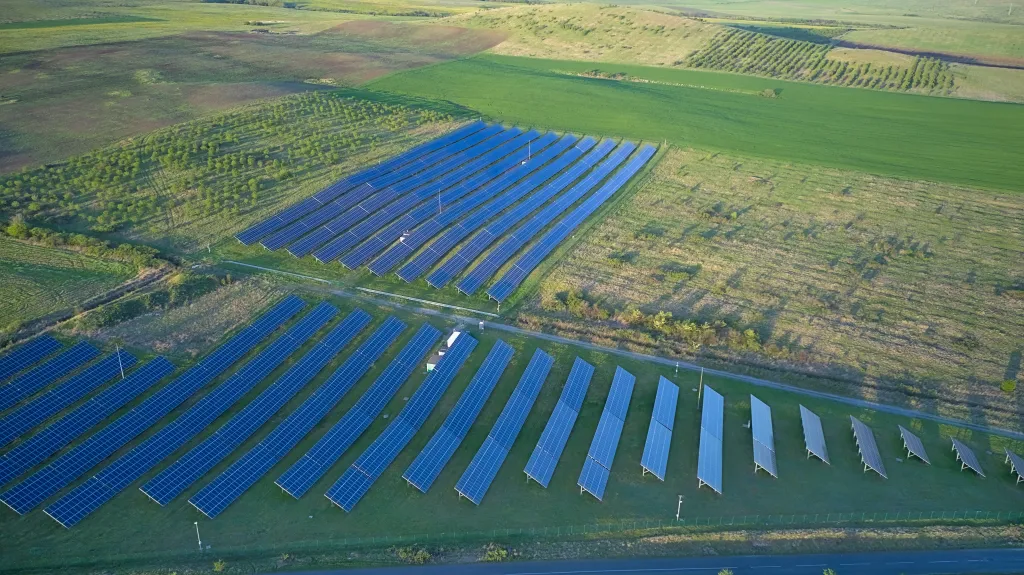
Corrosion Prevention for Power Generation: Protecting Critical Equipment
Power generation facilities operate in harsh and demanding environments, making corrosion prevention for power generation a critical concern. Components in biomass energy plants, hydroelectric power plants, solar power energy systems, geothermal facilities, and wind power systems face continuous exposure to moisture, fluctuating temperatures, airborne contaminants, and harsh chemicals. If left unchecked, corrosion can lead to
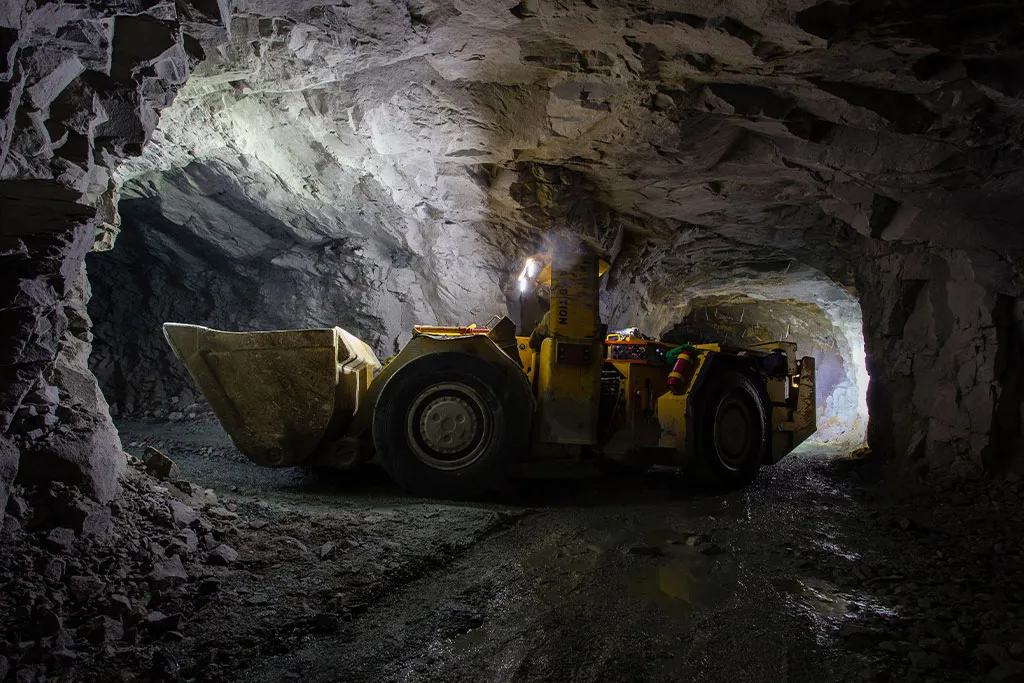
Addressing Corrosion Challenges in the Mining Industry with ZERUST® Solutions
The mining industry faces persistent challenges from corrosion, which is a natural degradation process exacerbated by harsh environments. Consequently, corrosion impacts equipment, safety, and profitability. Therefore, implementing proactive solutions is essential. In addition, this blog explores how ZERUST®’s corrosion prevention and remediation products address corrosion challenges in the mining industry. Corrosion Challenges in the Mining
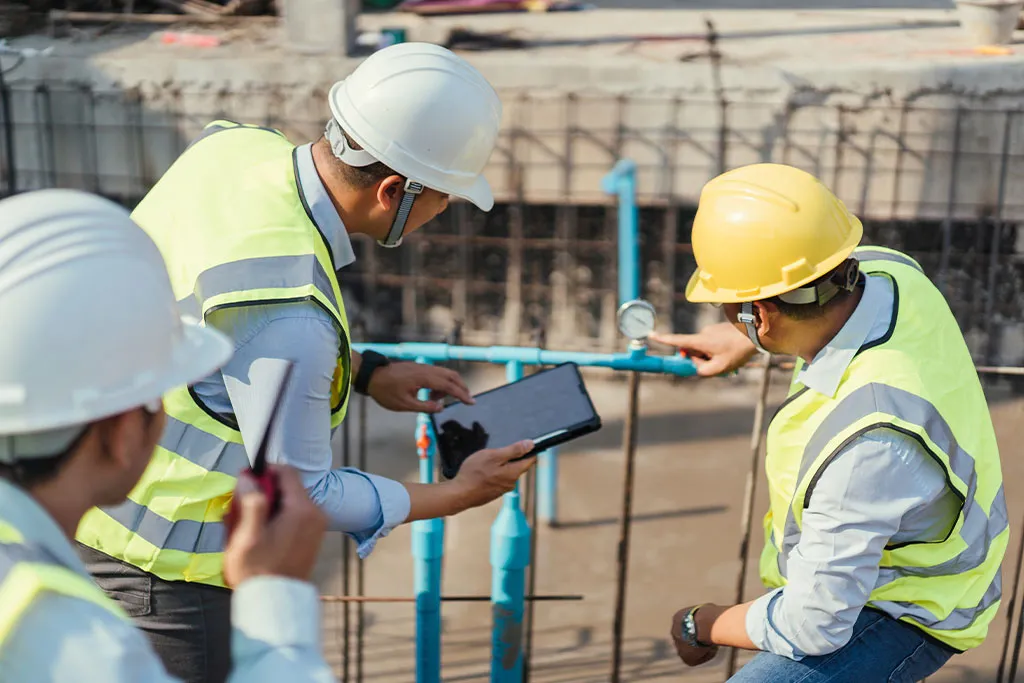
Hydrostatic Pressure Testing vs. Pneumatic Pressure Testing: Choosing the Right Method for Your Pipeline
When evaluating the integrity and safety of pressurized systems, two widely used methods are pneumatic and hydrostatic pressure testing. For industries such as oil and gas, pipeline integrity is critical. Selecting the right method can ensure safety, accuracy, and cost-efficiency. This blog will focus on the benefits and challenges of each testing method, emphasizing the
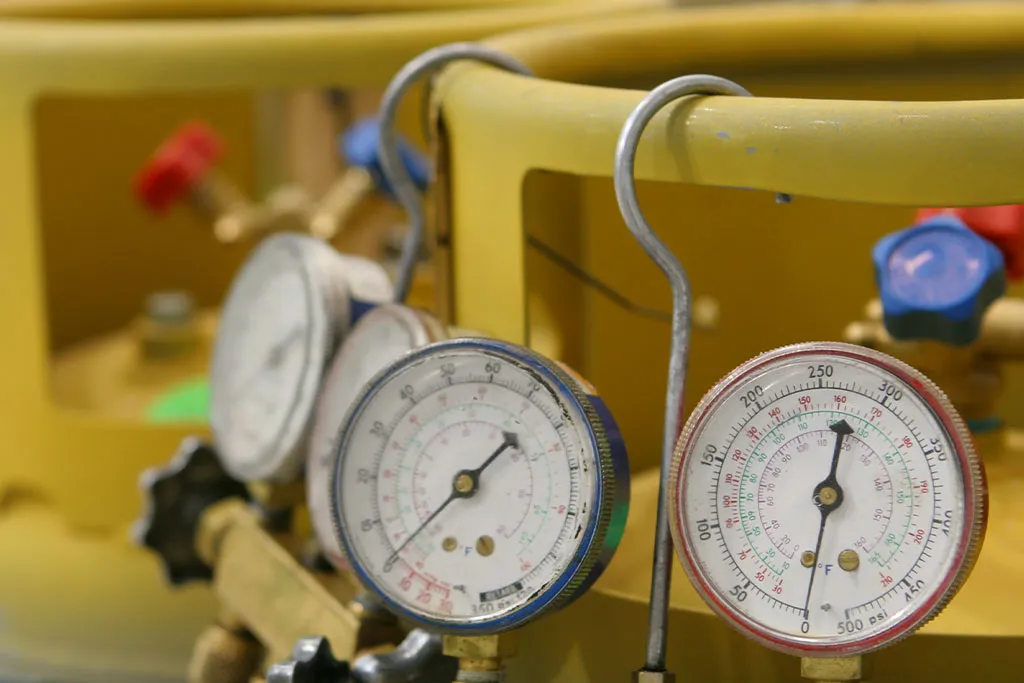
Comprehensive Guide to Hydrostatic Testing: Definition, Process, Advantages, and Corrosion Protection Solutions
What is Hydrostatic Testing Hydrostatic testing is a technique used to verify the durability of pressure vessels, pipes, and other equipment, essential for detecting leaks and ensuring the structural integrity of these components. By filling items with water and pressurizing them, industries can ensure these assets will endure operational stresses. Purpose and Applications
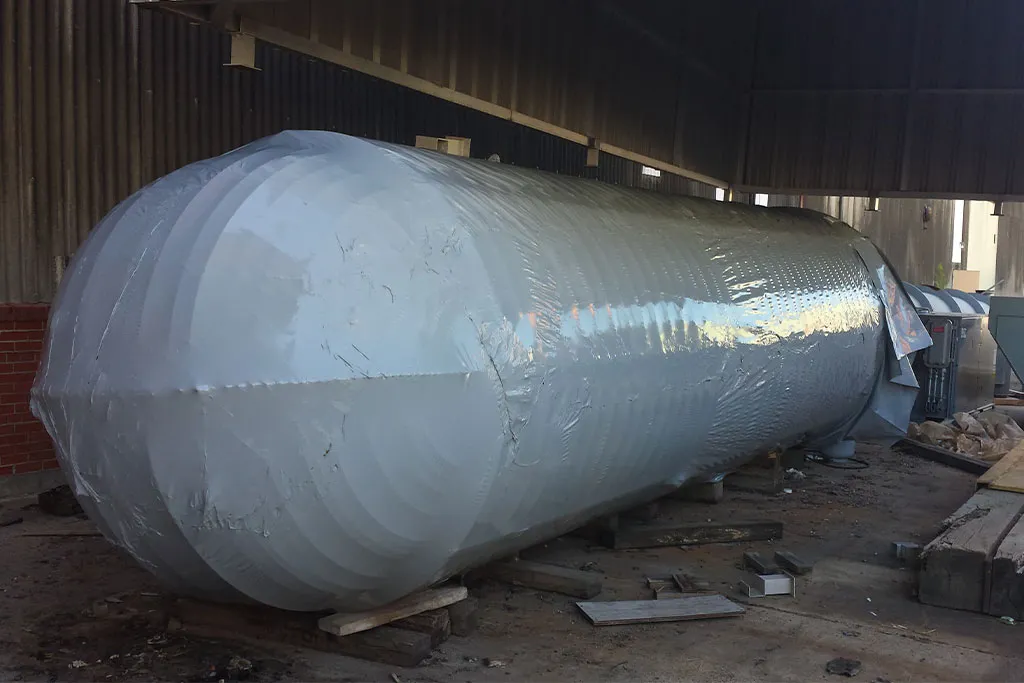
Comprehensive Guide to Heat Exchanger Corrosion Protection
Heat exchangers are critical components in various industries, responsible for transferring heat between fluids to regulate temperature and ensure efficient system operation. Despite their importance, these systems often operate in challenging environments where exposure to humidity, fluctuating temperatures, and corrosive chemicals can lead to significant corrosion. Corrosion issues are particularly prevalent during outdoor storage and
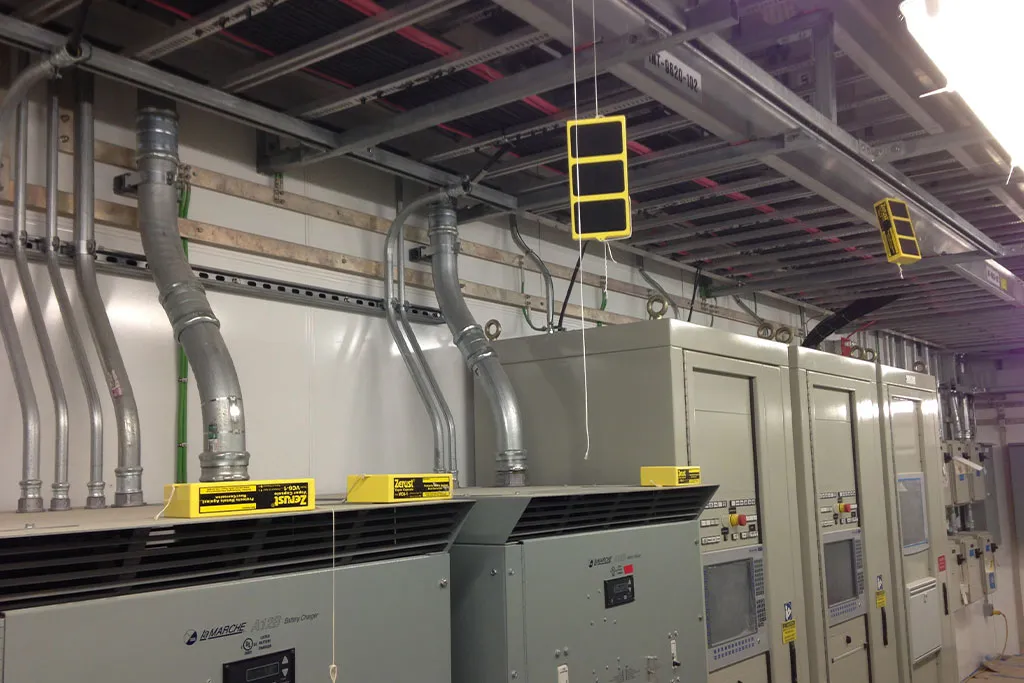
Corrosion Control for Control Rooms and Electronics: A Comprehensive Guide
Corrosion is a silent threat that plagues control rooms and electronics in industrial settings. As a result, it can cause circuitry failures, compromise equipment reliability, and ultimately lead to costly downtime. In this blog post, we’ll explore the challenges of corrosion control in control rooms and electronics and how innovative products like ZERUST® ActivDri™ Packets,